Presentation
MUSAM is an interdisciplinary research unit pushing the frontier of mechanics beyond the existing boundaries through the integration of computational and experimental mechanics, numerical analysis and materials science. Frontier research topics include solid and fluid dynamics for industrial problems, mechanics for sustainable paper and paperboard solutions, coupled problems in engineering science, renewable energy systems, and innovative digital technologies applied to cultural heritage
The research unit addresses frontier research topics of high technological and cultural relevance, pursuing an interdisciplinary approach which integrates computational and experimental mechanics, numerical analysis and materials science to go beyond the traditional disciplinary boundaries
People
- Prof. Dr. Ing. Marco Paggi (Director), Full Professor
- Prof. Dr. Chiara Cappelli, Associate Professor (conjoint with Scuola Normale Superiore)
- Dr. Ing. Andrea Mola, Tenure-Track Assistant Professor
- Dr. Pietro Lenarda, Tenure-Track Assistant Professor
- Dr. Ing. Maria Rosaria Marulli, Assistant Professor, 01/11/2023-31/10/2026
- Ing. Vittorio Bauduin, Research Collaborator
- Ms. Irene Nesi, PhD student (Systems Science, Track in Computational Mechanics, cycle XL)
- Mr. Ali Shahid, PhD student (Systems Science, Track in Computational Mechanics, cycle XL)
- Ing. Habib Ur-Rehmaan, PhD student (Systems Science, Track in Computational Mechanics, cycle XL)
- Ing. Prayuktha Bendadi, PhD student (Management of Digital Transformation, cycle XL)
- Ing. Syed Muhammad Zubair Shah Bukhari, PhD student (Systems Science, Track in Computational Mechanics, cycle XXXIX)
- Ing. Hassaan Idrees, PhD student (Systems Science, Track in Computational Mechanics, cycle XXXIX)
- Ing. Lorenzo Pasquetti, PhD student (Management of Digital Transformation, cycle XXXIX, scholarship co-funded by Nemesys SrL)
- Mr. Gabriel Cassese, PhD student (Systems Science, Track in Computational Mechanics, cycle XXXIX)
- Ing. Alice Bertolini, PhD student (Management of Digital Transformation, cycle XXXVIII, scholarship co-funded by Lucart SpA)
- Ing. Luca Cattarossi, PhD student (Management of Digital Transformation, cycle XXXVIII, scholarship co-funded by ToolsPole SrL)
- Ing. René Thierry Djoumessi, PhD student (Systems Science, Track in Computational Mechanics, cycle XXXVIII)
- Ing. Mohadeseh Fallah Yakhdani, PhD student (Systems Science, Track in Computational Mechanics, cycle XXXVIII)
- Mr. Mazhar Shehzad, PhD student (Systems Science, Track in Computational Mechanics, cycle XXXVIII)
- Ing. Ajinkya Dusane, PhD student (Systems Science, cycle XXXVI)
- Ing. Karthik Ambikakumari Sanalkumar, PhD student (Systems Science, cycle XXXVI, Marie Curie Early Stage Researcher at University of Seville, double degree with IMT)
Former staff & placement: visiting professors and researchers, alumni and former collaborators.
Four enrolled PhD students describe their research activities and experience in short storytelling videos, see here.
Research topics
High-fidelity computational models for surface interactions
HPC algorithms (BEM, FEM, multi-scale BEM-FEM models) for contact problems involving surface roughness and texture, friction,
adhesion, wear, thermo-elasticity; topological characterization of natural and artificial rough surfaces with experimental techniques.
Numerical simulation of contact problems (PI: Dr. Maria Rosaria Marulli & Prof. Marco Paggi, IMT School)
Mechanics of complex network materials
Mechanics of paper and paperboard materials; recycling solutions for paper production waste;
innovative solutions for packaging based on cellulose fibers alternative to wood; biodegradable packaging solutions;
stastistical mechanics of cellulose materials; nonlinear continuum mechanics; in-situ mechanical testing.
In-situ testing of paper (top), computational modelling of the anisotropic nonlinear response of paper (bottom) (PI: Prof. Marco Paggi, IMT School)
Phase-field modelling of fracture
Development of phase-field models for fracture for visco-elastic, hyper-elastic, anisotropic polycrystalline materials and laminates, in statics and dynamics.
Phase-field modelling of fracture in hyper-elastic shells (PI: Dr. Maria Rosaria Marulli & Prof. Marco Paggi, IMT School)
Multi-scale methods
Molecular dynamics simulation of fracture in Silicon and Graphene; coupling of molecular dynamics and finite elements; global-local approaches for fracture in composites.
Simulation of crack propagation in graphene-coated Silicon (PI: Prof. Marco Paggi, IMT School)
Mechanics of materials for renewable energy applications
Computational methods for durability assessment of photovoltaics and the design of innovative end-of-life recycling methods; image analysis techniques based on
electroluminescence and infrared imaging; phase field simulation of fracture in Silicon photovoltaics; Hydrogen production and storage technologies.
Electroluminescence images of photovoltaic modules showing damage within
the ERC Starting Grant project CA2PVM and the ERC Proof of Concept project
PHYSIC (PI: Prof. Marco Paggi, IMT School)
Computational fluid dynamics and reduced order models
Potential flow simulation for free surface flows with nonlinear boundary conditions; boundary element method solvers for ship hydrodynamics;
fluid-structure interaction models;
Navier-Stokes simulations for vortex induced vibrations in structures exposed to winds and streams; reduction of computational cost via intrusive and non intrusive reduced
order models; smoothed particle hydrodynamics and lattice Boltzmann method; applications to naval engineering, lubrication and biomechanics.
Computational fluid dynamics simulations for naval engineering applications (PI: Dr. Andrea Mola, IMT School)
Simulation of hydrodynamic lubrication (left) and flow of particles immersed in blood (right) (PI: Dr. Pietro Lenarda, IMT School)
Computational methods for coupled problems and biomechanics
Thermo-mechanics; piezoelectric materials and programmable materials; chemical degradation of polymers (adhesion, optical properties, etc.);
advection-reaction-diffusion systems; electro-physiology coupled with finite elasticity for digital twins of biological tissues and organs.
Digital twin models of the intestinal system (PI: Dr. Pietro Lenarda, IMT School), in collaboration with the ERC Consolidator Grant
MiGEM (PI: Prof. Alessio Gizzi, Campus Biomedico of Rome)
Computational archaeology
Experimental characterization of wear traces in paleolithic ground stone tools; digital-twin model of ground stone tools.
Digital-twin model of ground stone tools (PI: Dr. Giusi Sorrentino, Università Ca' Foscari & Dr. Maria Rosaria Marulli, IMT School)
Data driven analysis of handwritten artifacts
Artificial neural networks for the analysis of ancient handwritten manuscripts; experimental methods for morphological analysis of ancient materials.
Example of ancient manuscripts analyzed using artificial neural networks within
the ERC Starting Grant project UnMaP
(PI: Prof. Silvia Di Vincenzo, Università Ca' Foscari)
Laboratory
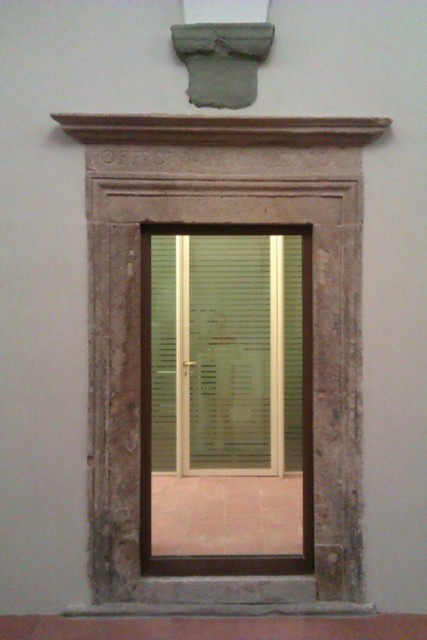
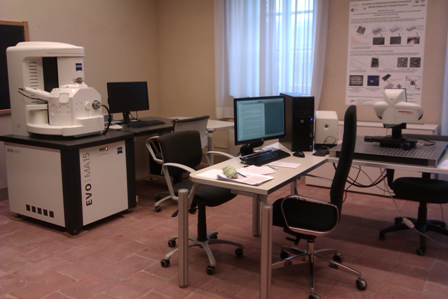
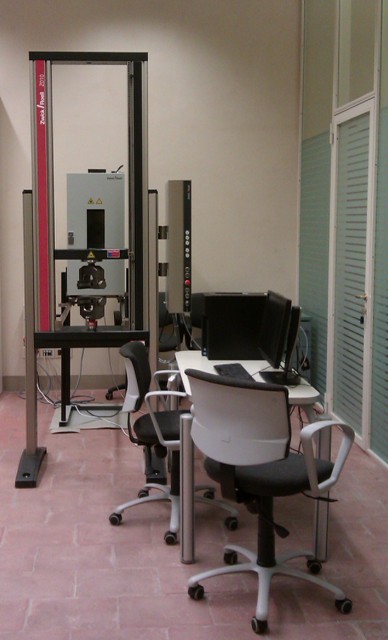
MUSAM-Lab - experimental laboratory for materials testing, see more on its web-site
Opportunities for industrial collaborations (in Italian):
Leaflet of the MUSAM-Lab
The laboratory is currently involved in technology transfer projects with national and international companies. Please contact Prof. Marco Paggi (marco.paggi@imtlucca.it), Director of the lab, for R&D contracts.
Events
Advanced courses and seasonal schools
- PRO Winter School of the NewFrac Marie Curie ITN Project, 7-11 February 2022, IMT School for Advanced Studies Lucca.
- Advanced Course Modelling and Simulation of Tribological Problems in Technology, CISM International Centre for Mechanical Sciences, 28 May-1 June, 2018, Udine.
- 2nd Summer School of the Italian Association of Tribology, 28 August-1 September, 2017, Salerno.
Conferences and workshops
- New Horizons In Structural Mechanics, Elasticity and Homogenization, 28-31 July 2025, IMT School for Advanced Studies Lucca. , IMT Lucca, 9-12 May 2022, IMT School for Advanced Studies Lucca.
- Expanding Horizons, Workshop of the NewFrac Marie Curie ITN Project, 9-12 May 2022, IMT School for Advanced Studies Lucca.
- GIMC-GMA 2016 Joint Conference of the Italian Group of Computational Mechanics and of the AIMETA Group on Materials, 27-29 June, 2016, IMT School for Advanced Studies Lucca.
- EUROMECH Colloquium 575 Contact Mechanics and Coupled Problems in Surface Phenomena, March 30-April 2, 2015, IMT School for Advanced Studies Lucca.
- Seminar on metallic and ceramic materials with applications to paper industry, in cooperation with ASM International and Confindustria Toscana Nord, 26 May, 2016, IMT School for Advanced Studies Lucca.
Collaborations
External academic collaborations
The research unit collaborates with several research centers, universities, and institutions around the World and in Italy, including:
- Prof. D. Bigoni, University of Trento (Italy)
- Prof. M. Corrado, Prof. S. Grivet Talocia, Prof. F. Spertino, Politecnico di Torino (Italy)
- Prof. P. Camanho, University of Porto (Portugal)
- Prof. J. Reinoso, Prof. V. Mantic, Prof. I.G. Garcia University of Seville (Spain)
- Dr. A. Turon, University of Girona (Spain)
- Prof. D. Dini, Imperial College London (UK)
- Prof. D.A. Hills, University of Oxford (UK)
- Prof. F. Borodich, Cardiff University (UK)
- Prof. J.R. Barber, University of Michigan (Michigan, USA)
- Prof. J.Q. Wang, Northwestern University (Illinois, USA)
- Prof. P. Wriggers, Leibniz University of Hannover (Germany)
- Prof. A. Popp, Universitaet der Bundeswehr Munich (Germany)
- Prof. R. Rolfes, Leibniz University of Hannover (Germany)
- Prof. S. Gorb, University of Kiel (Germany)
- Prof. R. Brendel, Dr. S. Kajari-Schröder, Institute for Solar Energy Research Hamelin (Germany)
- Prof. T. Rabczuk, Bauhaus University of Weimar (Germany)
- Prof. V. Popov, Technical University of Berlin (Germany)
- Dr. P.B. Ramaiah, Indian Institute of Technology Bhubaneswar (India)
- Prof. N. Datla, Indian Institute of Technology New Delhi (India)
- Prof. Q.-C. He, Laboratoire de Modélisation et Simulation Multi Echelle of the University of Paris-EST (France)
- Prof. J.-F. Molinari, Ecole Polytechnique Fédéral de Lausanne (Switzerland)
- Prof. O. Naimark, Dr. O. Plekhov, Institute of Continuous Media Mechanics of the Russian Academy of Sciences (Russia)
Industrial collaborations
MUSAM is promoting technology transfer in cooperation with the Joint Technology Transfer Office (JoTTO). Since 2013, MUSAM has activated technology transfer projects abd collaborations with the following industrial partners:
- Lucart S.p.A. (Porcari (LU), Italy)
- ToolsPole (Tallinn, Estonia)
- Sigma Ingegneria S.R.L. (Lucca, Italy)
- Robert Bosch GmbH (Renningen, Germany)
- LUCENSE SCaRL (Lucca, Italy)
- CROMOLOGY Italia S.p.A. (Porcari (LU), Italy)
- Tacchificio Villa Cortese S.r.l. (Villa Cortese (MI), Italy)
- Euro Inn Advisory S.r.l. (Correggio (RE), Italy)
- CIEFFEPI S.r.l. (Pistoia (PT), Italy)
- Solbian Energie Alternative S.r.l. (Avigliana (TO), Italy)
- Applied Materials Italia S.r.l. (Olmi di S. Biagio di Callalta (BO), Italy)
- Jabil, Industrial and Energy (San Petersburg, Florida, USA)
Selected publications co-authored by industrial partners:
- H. Zarei, M.R. Marulli, M. Paggi, R. Pietrogrande, C. Üffing, P. Weißgraeber (2020) Adherend surface roughness effect on the mechanical response of silicone-based adhesive joints, Engineering Fracture Mechanics, 240, 107353.
- H. Zarei, M.R. Marulli, M. Paggi, R. Pietrogrande, C. Üffing, P. Weißgraeber (2020) Mechanical characterization and failure modes in the peeling of adhesively bonded strips from a plastic substrate, Mechanics of Advanced Materials and Structures, 1-6.
- M. Paggi, I. Berardone, M. Martire (2016) An electric model of cracked solar cells accounting for distributed damage caused by crack interaction, Energy Procedia, 92C:576-584 doi:10.1016/j.egypro.2016.07.022
- V. Gade, N. Shiradkar, M. Paggi, J. Opalewski (2015) Predicting the long term power loss from cell cracks in PV modules, IEEE 42nd Photovoltaic Specialist Conference (PVSC), June 14-19, 2015, New Orleans, USA, (p. 1-6), doi:10.1109/PVSC.2015.7355665
Projects and funding
Ongoing
- 2023-2027 - Research unit, Marie Skłodowska-Curie Staff Exchanges (HORIZON-MSCA-2021-SE-01) "Ductility and Fracture Toughness analysis of functionally graded materials - DIAGONAL", granted by the European Research Executive Agency (GA 101086342), 184,000 Euro, 48 months.
- 2020-2024 - Research unit, Marie Skłodowska-Curie Innovative Training Network (H2020 MSCA-ITN) "New strategies for multifield fracture problems across scales in heterogeneous systems for Energy, Health and Transport - NEWFRAC", granted by the European Research Executive Agency (GA 861061), 3,359,824.20 Euro, 48 months.
Closed
- 2022-2024 - Coordinator, NEXTPAPER4.0 "Next Generation Paper and Packaging", Fondo per lo Sviluppo e la Coesione della Regione Toscana, 60.000 Euro, 24 months, in cooperation with Lucense scarl.
- 2022-2023 - Coordinator, "Scientific computing for natural sciences, social sciences, and applications: methodological and technological development", funded by MUR, PRO3 joint programme of the Italian Schools for Advanced Studies, 595,800 Euro, 24 months.
- 2019-2023 - Research unit, Research Project of National Interest (PRIN 2017) "XFAST-SIMS: Extra fast and accurate simulation of complex structural systems", granted by the Italian Ministry of Education, University and Research (GA 20173C478N), 877,560 Euro, 36 months.
- 2018-2020 – Research unit, POR FESR 2014/2020, action 1.1.5 sub-action a1 - Call 1, Strategic Projects of Research and Development "GlycoG-Lab 4.0", 2,500,575 Euro, 24 months.
- 2018-2020 – Coordinator, MIUR-DAAD Joint Mobility Program 2017 "Multi-scale modeling of friction for large scale engineering problems". The project, in collaboration with Prof. Dr.-Ing. A. Popp (Bundeswehr Universität Munich) is granted by the Italian Ministry of Education, University and Research (MIUR), and the Deutscher Akademischer Austausch Dienst (DAAD), 40,000 Euro, 24 months.
- 2018-2020 – Project POR FSE 2014-2020 "PROPAINT" to support 1 post-doctoral research fellowship, co-funded by Tuscany Region and by the company CROMOLOGY ITALIA spa (Porcari (LU), Italia), 54,000 Euro, 24 months.
- 2016-2018 – Coordinator, ERC Proof of Concept 2016 "PHotovoltaic with SuperIor Crack resistance", granted by the European Research Council (149,500 Euro, 18 months).
- 2012-2017 – Coordinator, ERC Starting Grant 2012 "Multi-scale and multi-physics computational approach to design and durability of photovoltaic modules", granted by the European Research Council, 1,483,980 Euro, 60 months).
- 2013-2016 – Coordinator, FIRB 2010 Future in Research Project "Structural mechanics models for renewable energy applications", granted by Italian Ministry of Education, University and Research MIUR, 954,800 Euro, 48 months.
- 2011-2012 – Coordinator, Vigoni Project 2010 "3D modelling of crack propagation in polycrystalline materials". The project, in collaboration with Prof. P. Wriggers, Leibniz University Hannover, Hannover, Germany, is granted by the Italian Ministry of Education, University and Research (MIUR), Ateneo Italo-Tedesco, and the Deutscher Akademischer Austausch Dienst (DAAD), 15,000 Euro, 24 months.
Impact
The research output regards the publication of scientific results in top journals of physics, engineering and materials science. Most of them are co-authored by PhD students and are stemming from international cooperations.
Another important output concerns the formation of Ph.D. candidates capable of exporting the scientific skills acquired at IMT not only in other academic groups, but also into the industry,
which represents the best way to disseminate the methodologies developed in the research unit to industrial practice.
MUSAM-Lab included in Cartaditalia n.3 dedicated to "New frontiers of Italian scientific research"
Key figures (2013-2023)
- Supervised PhD students: 25
- Visiting PhD students: 5
- Best PhD thesis awards: 2
- Rectuited post-doc and research collaborators: 15
- Visiting professors and researchers: 12
- PhDs and post-docs co-funded by companies: 6
- Number of publications: 185
- % of publications with international co-authors: 49%
- % of publications co-authored by PhD students: 35%
- Organized seminars: 72
- Organized conferences, workshops and schools: 7
- Articles on newspapers mentioning MUSAM: 26
- TV interviews and youtube videos: 4
- Total attracted funds: 2.6 MEuro
- Projects’ funds at IMT Lucca: 2.6 MEuro
- Industrial contracts supporting research staff: 320 kEuro
- Patents: 1
- Spin-offs: 1
Follow MUSAM updates on its facebook fanpage since 2016: MUSAM on facebook
10-year impact report 2013-2023